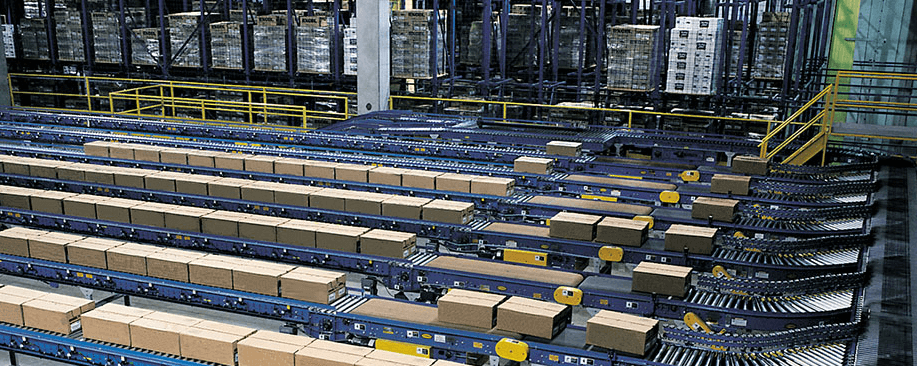
When looking at a slider bed, you’ll notice the large sheets of metal that act as a support for product under the belt. This makes for a smooth transport, but creates friction with the belt and requires more horsepower to run. A roller bed utilizes rollers under the belt, which creates less friction, uses less energy and requires fewer drives.
Of course every operation is a little bit different, but in general you should use the following guidelines when deciding which of these to implement in the parts of your solution.
Considering product types
I’ve said it before and I’ll say it again: always consider your product. It’s a no-brainer to invest in equipment that utilizes the least amount of energy and requires the least amount of maintenance to improve your total cost of ownership. That means that if possible, you’ll probably want to use a roller bed. This is true for regularly shaped products—boxes with even weight distributions, for instance—but it’s not true when you start conveying products with irregular shapes and weights.
Think of the small round shot puts that are used in track and field. These small spheres pack 16 pounds of weight that is all point loaded. When being conveyed on a roller bed, these items are prone to bouncing and turning. In this case, a slider bed would be your best option because it provides more stability and control for your product.
Inclines and declines
With regular products, there are two main rules for inclines and declines: use a roller bed for inclines and use a slider bed for declines.
Why? An incline requires more horsepower to be used, so you want the least friction between your belt and the rollers (if you must use a slider bed, use more horsepower and shorter lengths on the incline). However, with a decline, a slider bed is more appropriate. The friction between the belt and the bed keeps from working the brake motor too hard and keep your product speed controlled.
High-speed scan tunnels
This is an easy choice. Bad scans hurt throughput, and to get the highest scan rate possible, you want to make your product as stable as possible. In a scan tunnel, you should always use slider beds.
A note about belt friction
Always consider using belt friction to your advantage. Normally, you put the side of the belt with a smaller coefficient of friction on the bottom, in contact with the bed or rollers. There’s one big exception, and that is spurs. When products are pushed onto a belt from a spur, the lowest amount of friction should be on top, and the highest friction should be in contact with the rollers. This allows for a smooth transport of items onto the belt and lessens the danger of the boxes pushing the belt over and mistracking it.
These rules may seem like common sense, but to ignore them can sign you up for bad throughput and excessive downtime with your conveyor system. When considering your options, take a second look at the general rules above. They could save you from wasted money and frustration down the line.